The Ultimate Guide To Alcast Company
Table of ContentsThings about Alcast CompanyGetting The Alcast Company To WorkNot known Details About Alcast Company The Best Strategy To Use For Alcast CompanyAbout Alcast CompanyThe Only Guide for Alcast Company
The subtle difference hinges on the chemical material. Chemical Contrast of Cast Light weight aluminum Alloys Silicon advertises castability by reducing the alloy's melting temperature and enhancing fluidness throughout spreading. It plays a critical role in allowing elaborate molds to be filled up properly. In addition, silicon adds to the alloy's strength and put on resistance, making it valuable in applications where sturdiness is essential, such as auto components and engine parts.It additionally boosts the machinability of the alloy, making it less complicated to refine into completed products. In this means, iron adds to the general workability of aluminum alloys. Copper increases electric conductivity, making it helpful in electrical applications. It also boosts corrosion resistance and adds to the alloy's total toughness.
Manganese contributes to the strength of aluminum alloys and boosts workability (Foundry). It is commonly made use of in wrought aluminum products like sheets, extrusions, and accounts. The existence of manganese help in the alloy's formability and resistance to splitting during manufacture processes. Magnesium is a light-weight element that gives stamina and influence resistance to light weight aluminum alloys.
3 Easy Facts About Alcast Company Shown
It enables the manufacturing of light-weight components with exceptional mechanical homes. Zinc boosts the castability of light weight aluminum alloys and helps manage the solidification procedure throughout spreading. It boosts the alloy's strength and hardness. It is typically located in applications where intricate shapes and fine details are required, such as ornamental spreadings and particular auto parts.
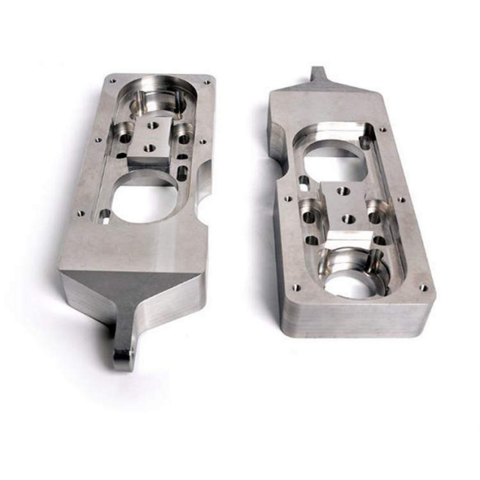
The key thermal conductivity, tensile strength, return strength, and prolongation vary. Amongst the above alloys, A356 has the highest possible thermal conductivity, and A380 and ADC12 have the cheapest.
The Of Alcast Company

In accuracy spreading, 6063 is appropriate for applications where detailed geometries and premium surface area finishes are critical. Instances consist of telecommunication enclosures, where the alloy's remarkable formability permits for sleek and visually pleasing layouts while maintaining structural stability. In the Illumination Solutions sector, precision-cast 6063 parts create stylish and efficient lighting fixtures that require elaborate shapes and good thermal performance.
It causes a better surface area finish and far better corrosion resistance in A360. The A360 displays remarkable prolongation, making it suitable for complicated and thin-walled elements. In accuracy casting applications, A360 is well-suited for industries such as Consumer Electronics, Telecommunication, and Power Devices. Its boosted fluidness permits complex, high-precision parts like smartphone casings and communication tool real estates.
See This Report on Alcast Company
Its distinct residential properties make A360 a beneficial choice for precision casting in these industries, enhancing product sturdiness and high quality. Foundry. Aluminum alloy 380, or A380, is a widely used casting alloy with several unique attributes.
In accuracy casting, light weight aluminum 413 radiates in the Consumer Electronic Devices and Power Equipment industries. This alloy's premium rust resistance makes it an outstanding choice for exterior applications, guaranteeing long-lasting, sturdy products in the stated markets.
See This Report on Alcast Company
Once you have determined that the aluminum die casting procedure appropriates for your job, a crucial next action is deciding on the most proper alloy. The light weight aluminum alloy you choose will significantly influence both try these out the casting process and the residential properties of the last product. Because of this, you need to make your choice carefully and take an educated technique.
Establishing the most appropriate aluminum alloy for your application will certainly imply evaluating a vast variety of qualities. The very first category addresses alloy features that affect the production procedure.
The Single Strategy To Use For Alcast Company
The alloy you pick for die spreading directly impacts several elements of the spreading process, like just how easy the alloy is to deal with and if it is prone to casting flaws. Hot splitting, also understood as solidification cracking, is a common die spreading defect for light weight aluminum alloys that can result in interior or surface-level rips or cracks.
Particular light weight aluminum alloys are extra vulnerable to warm fracturing than others, and your option must consider this. It can harm both the cast and the die, so you must look for alloys with high anti-soldering homes.
Rust resistance, which is currently a noteworthy quality of light weight aluminum, can differ substantially from alloy to alloy and is an important characteristic to think about depending upon the environmental conditions your product will be exposed to (aluminum foundry). Use resistance is one more building frequently looked for in light weight aluminum products and can distinguish some alloys